Stick welding can be done with different metals. But can you stick weld aluminum? Yes, it is possible to stick weld with aluminum metal.
Welding with aluminum is more challenging than steel welding. Having the proper equipment and knowing the techniques to do this tricky task is important. It would help if you were experienced and patient to weld with aluminum because it might be messy.
In this guide, we will explain whether are aluminum welding possible, the considering things of it and the details of the aluminum welding process.
Can You Stick Weld Aluminum?
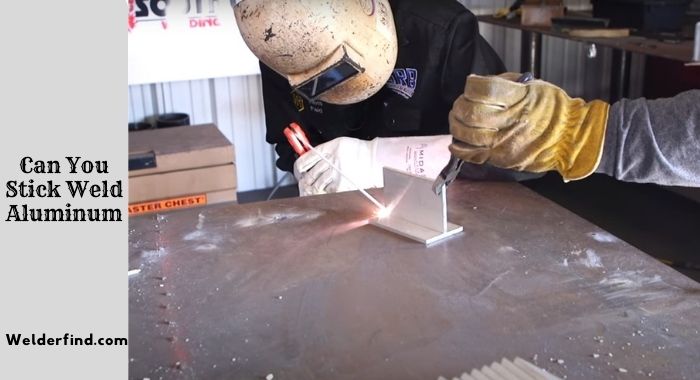
Stick weld aluminum metal is possible but more challenging than other metals. First, you must know the difficulties or disadvantages of using aluminum metal for welding. Secondly, knowing about ideal equipment, welding techniques, joint methods and setting preparation is required.
Besides, you need to know this method’s proper electrode type, electric amperage and precautions. Although aluminum welding is possible, they are quite difficult and not worthy of the user’s efforts.
How To stick welding aluminum?
Here is the step-by-step guide to stick welding aluminum.
Step 1: Assemble the welding equipment
You need to gather two materials, one for your safety guard and another for welding. The safety guard types of equipment are included safety glasses, welding helmet, earmuffs, thicker hand gloves, welding respirator, fire-resistant dress and leather boots.
On the contrary, the welding equipment is a DC stick welder, soap-like suitable alkaline product, stainless steel brush, chipping hammer, clean file and flame torch. So, arrange all of the equipment.
Step 2: Choose an ideal aluminum rod
You can weld aluminum with the same welding stick used for steel welding.
However, it would help if you had special welding aluminum with core wire and flux coating. E4043 is the most common welding aluminum that can weld on aluminum alloy 6061, 5052, 3003 and aluminum casting 355, and 356.
Good to know that the E4043 contains 5% silicone that can easily melt and is suitable for high heat without cracking. The welding aluminum 1100 is another good option for corrosion-resistant aluminum welding.
Step 3: Remove all dirt
Different types of dirt and aluminum may accumulate on the workpieces. Although metal welding is possible on dirty surfaces, you must clean the aluminum workpieces.
First, use soap or acetylene-based solvent to remove grease, cutting fluids and oil. A stainless-steel brush or carbide bur must be used to remove oxide from the workpieces. Besides, disk-made stainless-steel wire is great for removing stubborn dirt.
Step 4: Prepare the aluminum joint
Cut the workpieces into a bevel shape to make a v-joint between the two pieces. The bevel shape is also good for hot crack prevention. Good to know the common thickness of bevel joint is 3/16″ to 1/8″. So, angle 35° up to 45° for each side bevel.
It is recommended to clean the workpieces after cutting. You especially need to clean the workpieces after using plasma-cutting-like hot methods.
Step 5: Set up the polarity
Must use a DC+ polarity for stick welding with aluminum. Remember that DC-polarity is unstable, noisy and responsible for creating inconsistent beads.
Step 6: Set up the amperage
Aluminum metal has a low melting point. So, it is crucial to use the ideal amperage for aluminum welding. The ideal amperage is related to rod thickness, workpiece thickness and temperature. Let’s know the amperage range for Welding rod E4043.
Welding rod E4043 | Amperage |
3/32″ | 50-80 |
1/8″ | 70-120 |
5/32″ | 100-160 |
3/16″ | 130-200 |
Step 7: Inverter stick setting
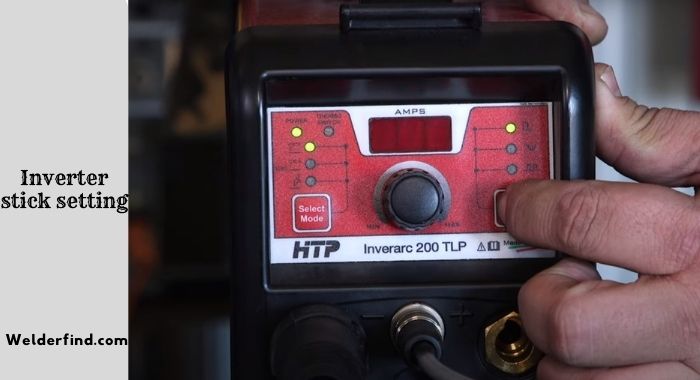
Hot-start and arc-force are two common features of stick welders. Hot-start increases the amperage without preheating. On the other hand, the arc-force feature increases the amperage when the arc length is less. TIG stick welding machine can deliver you the pulsed current.
Step 8: Get the Right Arc Movement
Arch movement should be done within a short time. Although some people think the arch movement is a personal issue, it should be faster.
Step 9: Use the correct angle
You should tip the electrode and keep it in a medium steep. The too-steep electrode hurts welding.
Step 10: End of The Weld
Take sometime after welding to fill the termination point. Check the welding surface to see if there have some craters on that. If you got some crates, then fill them.
Challenges of stick welding aluminum
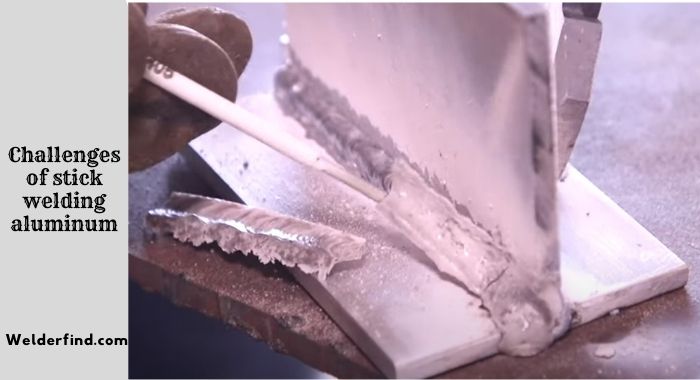
Stick welding with aluminum is a challenging process. Let’s know the common challenges of this process.
Oxidation
Aluminum might oxidize quickly with a touch of atmosphere. You will see a thin oxide layer on the welding surface at 2072 C° higher temperature.
Porousness
Tiny voids or bubbles may create on the aluminum welding surface due to the high amount of absorbed hydrogen. It may cause pressure and stress failure.
Impurities
Oil, dirt, air and debris hurts aluminum welding. Discoloration, graining, and corrosion are common impurities of aluminium stick welding.
Thickness
Aluminum welding is related to the different welding materials with unique thicknesses. So, it is tricky to weld with the combination of thicker and thinner materials.
Hot Cracking
A high level of temperature can cause hot cracking on aluminum weld. Due to hot cracking, once-arch aluminum was considered for stick welding.
Thermal Conductivity
Aluminum is a high-conductive metal that makes the joint in stick welding difficult. The thermal conductivity absorbs and ruins the heat rapidly.
Advantages & Disadvantages of stick welding Aluminum
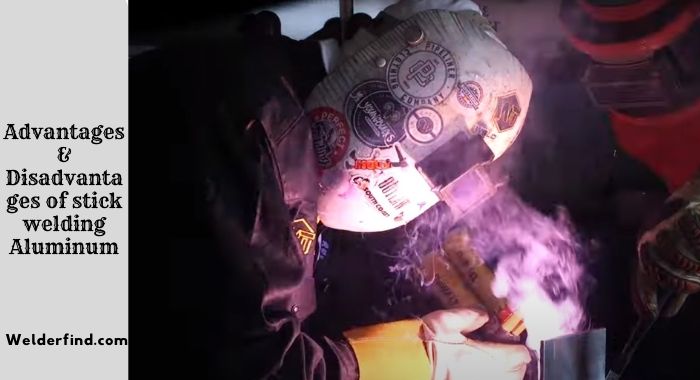
Stick welding has some core advantages and disadvantages. Knowing these can help you in stick aluminum welding.
Advantages
- Aluminum stick welding is suitable for adjusting with different types of welding material. So, you can change the electrode and adjust the welding easily. When you have multiple welding rods, it would be easier to change the electrode. The variety’s adjustability will make the whole process efficient and easier.
- You won’t need shielding gas in aluminum welding because the stick welder can produce Carbon dioxide gas.
- Stick welding can be without additional equipment like MIG and TIG welding processes. You only need a stinger lead and ground lead. However, it would help to have a box of sticks with various metals.
- Noise pollution in aluminum stick welding is very low.
- So where loud noise is causing trouble to neighbors or anyone else, stick welding can be done there.
- Aluminum stick welding is portable and easy to use anywhere with its own produced gas.
- The setting up and equipment cost of stick welding is affordable
- It doesn’t require expensive equipment like shielded gas cylinders, hoses, or preparation
Disadvantage
Stick welding is a naturally smoky process. You will especially feel suffocating if stick welding in any confined or narrow space.
- Stick aluminum welding is a comparatively slower process. Due to the slow process, it is restricted or prohibited in different industries where they need fast productivity.
- The material used in stick welding is generally moisture-resistant. I can cause damage if the set is stick-welded in the atmosphere.
- Due to the manual system, it isn’t easy to speed up the stick welding process with aluminum
- Stick welding is difficult with thicker metal or welding on a certain position.
- Forming slag is a common issue in stick welding because it can reduce the quality of stick welding.
- Slug remaining during welding can cause hazards if not removed properly.
- Stick welding is more difficult with thinner materials than is possible with other welding like TIG and MIG welding.
Last Words
It is possible to stick welding with aluminum metal, but not recommended. Aluminum stick welding is related to various challenges. Besides, it is a time-consuming process. If you want to stick welding with aluminum, gather proper knowledge, skills and experience.
Besides, knowing the core advantages and potential disadvantages is important before starting stick welding with aluminum. Otherwise, stick aluminum welding would be difficult for you.