Aluminum plate has a lot of benefits that make it a popular metal in the world. Most important characteristics of an aluminum plate is its hardness to weight ratio, means the metal is hard at the same time very light which make it a unique metal.
Normally an aluminum which is less than a quarter (1/4)” is called sheet aluminum. Any thickness greater than 1 quarter is called plate aluminum. A half inch (1/2)” aluminum and a 3/8″ aluminum are plate aluminum.
Today we will talk about tig welding settings for that 1/2″ aluminum.
Lets start-
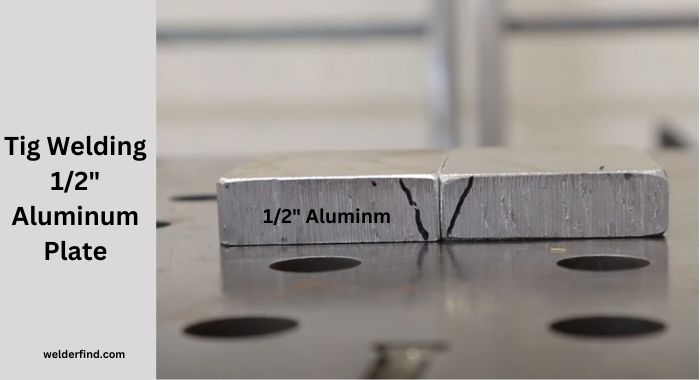
Aluminum Type Used For Tig Welding
Generally 6061 aluminum plate is used for tig welding work. Because 6061 aluminum is most versatile type of aluminum. It can be used in a wide range of applications from trailers of vehicles to aerospace industries.
The metal’s main alloying agent is magnesium and silicon. Precipitation hardening technique is used to roll the metal that increase its toughness. Its tensile strength is 45000psi and elongation rate is 12%.
Its most important feature is its weldability which makes it a tig welding friendly metal. Tough it is weldable, sometimes it can lose its strength as a result of welding. Further heat treatment is required to re-strengthen then metal.
Tig Welder To Use
You may use AC tig aluminum welder of 400-450 amp power with 210v input. A 3/16″ tungsten, 5/8″ torch cup (water-cooled) and 3/16″ filler metal is required with the welder to tig weld 1/2″ aluminum plate perfectly. 2-3 passes of welding may be required with 8-10 ipm travel speed for tig welding 1/2 inch aluminum.
Settings For Tig Welder
We will mention tig welder settings to weld 1/2″ aluminum in Lap, Butt, Corner & Filler joint welding.
Butt Welding (Settings)
Features | Settings |
---|---|
Tungsten Diameter | As 1/2″ is thicker material, you should use 1/8″ or 5/32″ tungsten to butt weld. 2% ceriated (orange) is better for welding thick metals. |
Torch Cup | Use 5/8″ water-cooled torch cup |
Filler Metal | 1/8″ filler metal would be best for 1/2″ aluminum welding |
Amperage | You may 120-290amp but you will need to weld in 5 passes. If you use 400-450 amp welder, then 2 passes would be enough. |
Gas & Flow rate | You may use argon gas @ 31 cft |
Weld Speed | It cannot be predicted because depending on your welders amperage you would need to apply multiple pass. For 290-290amp 1 root pass, 2nd pass for 150-170amp, 3rd for 140-160amp, 4th for 130-150amp and 5th for 120-140amps. |
Lap Joint (Settings)
Features | Settings |
---|---|
Tungsten | Same as butt joint requirement |
Torch Cup | Use 5/8″ water cooled torch cup like butt joint |
Filler | Same as butt that is 1/8″(3.2mm) |
Amperage | Use 280-320amp Ac welder. |
Gas & Flow Rate | Argon at 31cft |
Speed | Required more than 2 pass for 280-320 amp. If you can increase the amperage to 400amp then 2 pass would be enough |
Corner Weld (Settings)
Features | Settings |
---|---|
Tungsten | 2% ceriated (orange) tungsten of 1/8″(3.2mm) or 5-32″(4mm) would be good |
Torch Cup | 5/8″ water cooled cup is enough |
Filler | Same as butt and lap joint |
Amperage | You may use welder amperage ranging from 145 to 300 amp |
Gas & Flow Rate | Same as butt and lap joint |
Travel Speed | Travel speed varies depending on amperage. For using 145-300amp welder, you may need 6 passes to complete the joint. For 270-290amp first root pass and all remaining for 145-165amp. |
Fillet Joint ( Settings)
Features | Settings |
---|---|
Tungsten | Same to butt and lap joint |
Torch Cup | 5/8″ water cooled torch cup is preferred |
Filler | 1/8″ filler metal |
Amperage | Amperage should be 320-350amp. Not less than that. 400-450amp would be best. It would reduce the necessity of extra pass. |
Travel Speed | 3 passes with 320-350amp welder |
The above mentioned settings are approximated. It may differ based on welder machine and brands. Please check out the product manual before starting to weld.
Last Words
It maybe difficult to weld 1/2 inch aluminum because of its thickness. You may need to weld a single joint multiple times based on amperage and power.
What ever the application, the above mentioned settings will hopefully help you set your welder and other accessories & prepare you to weld 1/2″ thick aluminum effectively.